#07
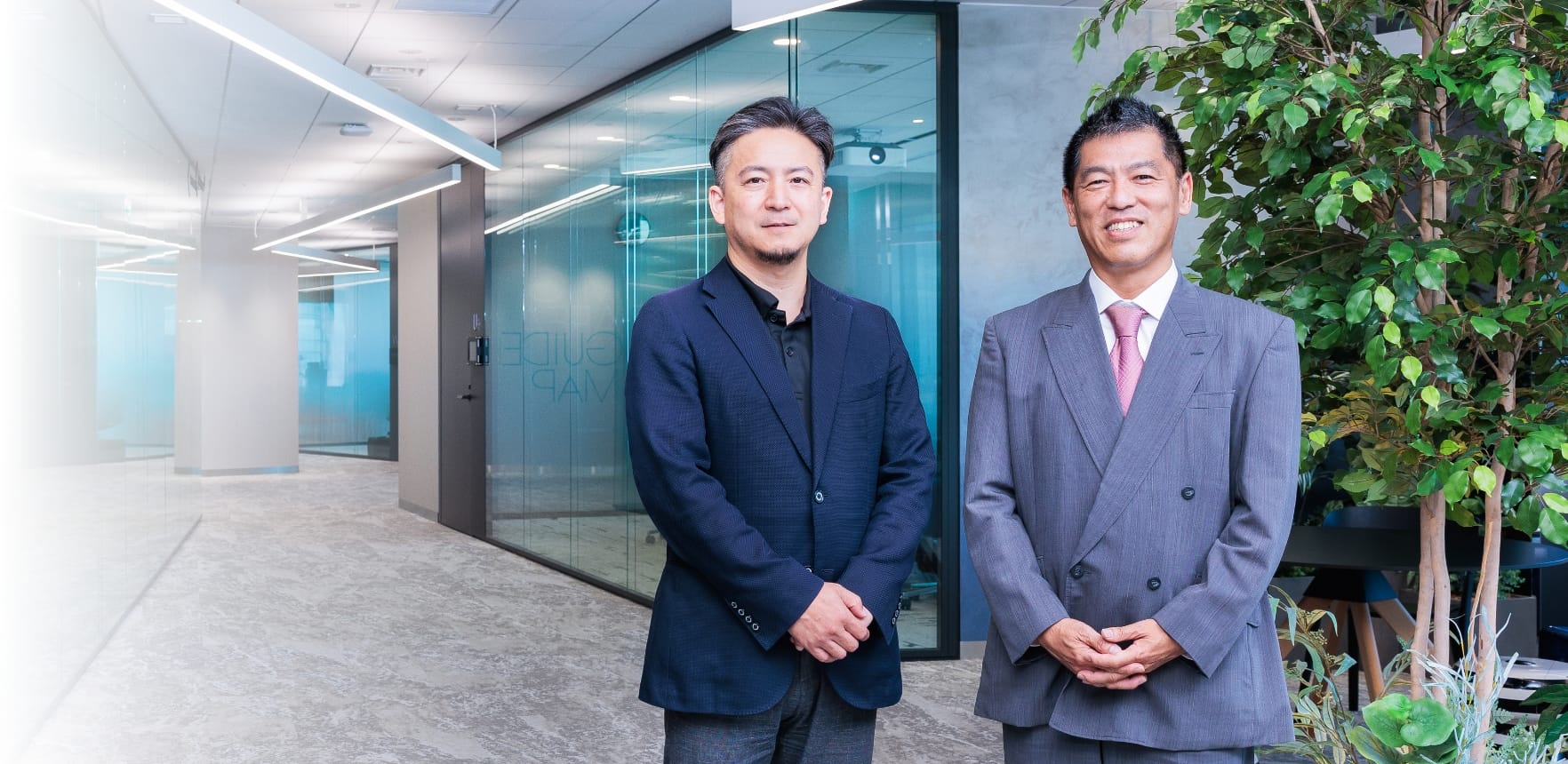
- 八子 知礼
- 株式会社INDUSTRIAL-X
- 代表取締役CEO
- 名畑 英二
- クオリカ株式会社
- ビジネスイノベーション事業部
副事業部長
ITで現場を見える化し、つなげることで製造現場に新たな価値を。
製造現場にもDX(デジタルトランスフォーメーション)の波が押し寄せています。人手不足や働き方改革を意識した生産性の向上、あるいはGHG(温室効果ガス)の排出量削減など、解決すべき課題が山積みで、デジタルを活用したこれまでにない新しい発想が求められています。
本記事では株式会社INDUSTRIAL-X代表取締役CEOの八子知礼さんをお招きし、クオリカ株式会社・名畑英二と「製造現場×ITで実現したい未来」について対談を行いました。
本記事では株式会社INDUSTRIAL-X代表取締役CEOの八子知礼さんをお招きし、クオリカ株式会社・名畑英二と「製造現場×ITで実現したい未来」について対談を行いました。
「DX推進が製造現場にこれまでにない新しい価値を生み出す」
「DX」という言葉が製造業界においても広まってきていますが、具体的にどういったものかイメージが湧きづらく、推進が難しいところがあります。お二人はどのような意味合いで捉えていますか?
名畑さん
(以下、敬称略)
(以下、敬称略)
八子さんのおっしゃる通りで、デジタル化によってペーパーレスを実現するなど、効率化して生産性を向上することができていても、新しいビジネスを生んでいるわけではありません。その認識の違いが、ときにお客様と私たちの間で、すれ違いを生じさせてしまいます。
デジタル化された現場の情報を、現場間、工場間、企業間、グローバル規模で共有・利活用することで新しい価値や新規ビジネスを生み出すことができます。しかし、DXを推進した先でいったいどんな効果が得られるのかまでイメージできなかったり、具体的な将来のメリットを想像できなかったりしているのが、製造現場においてDX推進を阻んでいる課題です。
デジタル化された現場の情報を、現場間、工場間、企業間、グローバル規模で共有・利活用することで新しい価値や新規ビジネスを生み出すことができます。しかし、DXを推進した先でいったいどんな効果が得られるのかまでイメージできなかったり、具体的な将来のメリットを想像できなかったりしているのが、製造現場においてDX推進を阻んでいる課題です。
工場などの製造現場でDXが推進されると、どのようなメリットがあるのでしょうか?
八子
スマートフォンの登場で、人々の生活は劇的に変わりました。旅行代理店に行かずともオンラインで移動手段や宿泊先の手配ができるようになったし、時計もポータブル音楽プレーヤーも財布も持たずに、スマートフォン1台にすべてが収まって行動できるようになりました。すべてが1台のデバイスで完結できる世界は、以前には想像もつかなかったもので、生活もビジネスも一変しました。
それと同じくらいの劇的な変化が、製造現場でも起きるのです。DXが浸透したあとの世界では、さまざまな産業において、スマートフォン上で工場の現場を確認し、オペレーション状況を把握できたり、あらゆるデータを掌握できることで意思決定がスムーズに行われていく。そんな未来が訪れるでしょう。
それと同じくらいの劇的な変化が、製造現場でも起きるのです。DXが浸透したあとの世界では、さまざまな産業において、スマートフォン上で工場の現場を確認し、オペレーション状況を把握できたり、あらゆるデータを掌握できることで意思決定がスムーズに行われていく。そんな未来が訪れるでしょう。
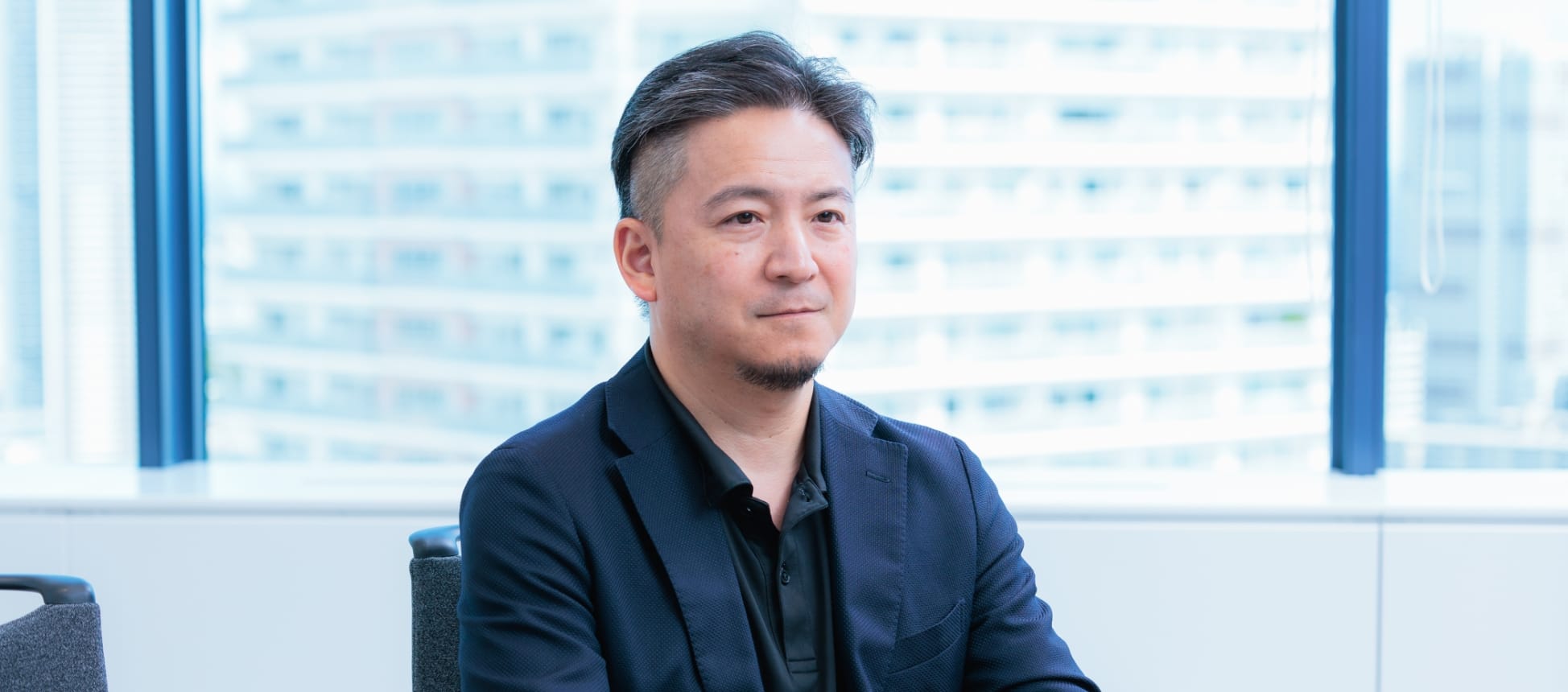
名畑
工場の中には30年以上も使われている機械があり、その動作状況をデジタル化するのは一苦労です。しかし、一つひとつの機械をオンラインで繋いでいけば、工場全体のデータを見える化できるようになります。ここが泥臭い作業で、皆さんなかなか手を出しづらいのですが、うまくデジタル化し、プラットフォームにデータを乗せれば、例えば現場に行かないと発見できなかった非効率な作業が、デバイス上で見えるようになる。データを集めることによって、生産性の向上やコストダウンができるようになるだけでなく、これまでにない新しい価値を生み出したり、品質向上に繋げられたりするのです。
「属人性や全体最適の発想の欠如が日本の製造現場の課題」
これまで工場などの製造現場が抱えていた課題感について、詳しく教えてください。
八子
日本の製造現場の課題は、端的に言うと「属人性」にあります。多くの現場では、マニュアルがあって手順も決まっているのに、作業時間がバラバラであることが少なくありません。生産管理システムを導入していても活用されず、膨大な量のエクセルで生産計画を作っている、などということもあります。しかし、品質は高いんですね。効率は良くないが、人の力でなんとかできてしまっている。そんなイメージです。
もう一つの課題は、生産設備が古いことです。効率が悪い上に、電力消費が激しい。あるいは、工場の自動化が進んでいたとしても、電子制御やデータ制御などの導入は極めて遅く、世界に比べて何周も遅れています。つまり、極めて生産性が低いのですが、その事実に気づいていない。そのことが、最大の課題ではないでしょうか。
もう一つの課題は、生産設備が古いことです。効率が悪い上に、電力消費が激しい。あるいは、工場の自動化が進んでいたとしても、電子制御やデータ制御などの導入は極めて遅く、世界に比べて何周も遅れています。つまり、極めて生産性が低いのですが、その事実に気づいていない。そのことが、最大の課題ではないでしょうか。
世界との差が開いてしまったのは、日本特有の問題があるのでしょうか。
八子
ここと決めたところだけを真面目に改善し続けてしまうんです。例えば、ある工程のある部門だけが大真面目に改善を続けることで120%のパフォーマンスを発揮できたとしましょう。大変素晴らしいことですが、前後の工程が60%のパフォーマンスのままだったら、それに引っ張られて、全体の生産性は一向に向上しません。
この場合、全体最適の発想と視点を持って、改善する必要があります。しかし、全体最適の発想がないために、かえって全体の生産性が悪化してしまうことがあるのです。
この場合、全体最適の発想と視点を持って、改善する必要があります。しかし、全体最適の発想がないために、かえって全体の生産性が悪化してしまうことがあるのです。
クオリカの工場生産性改善システム「KOM-MICS」は、生産現場のノウハウから生まれたそうですが、どのような経緯や課題感から生まれたプロダクトなのでしょうか。
名畑
「KOM-MICS」は、建設機械メーカーであるコマツで、設備の生産性を向上させるために始まったプロダクトです。私は、現場の工具の能率を上げたり、加工方法をガラッと変えたりするような、生産技術の研究を行っていました。現場への技術導入の際に工場長とお話をさせていただくと、例えば「ある工具1本の改善で、工場全体でいくら分の金額を改善できるのか」と指摘され、工場全体で使用される機械、プログラム、使用時間といった数値はほぼ把握できず、データの収集と分析に大変苦労をしました。つまり、見える化がまだまだ行われていなかったのです。
新入社員研修でタイムスタディ(どの工程のどの加工に何分間の時間がかかっているのかをストップウォッチで測る)が行われていたのですが、あるとき研修を終えた若手社員が、機械の中にパソコンが入っていますから、機械にいつ何が起こったのかを問い合わせればデータですべてを吸い上げられるのに、なんて無駄な作業をさせるんだ、と愕然としていました。それで2013年から開発が始まったのが「KOM-MICS」です。
コマツの部品の多くは社外の協力企業によるものですから、社外の工場も見える化が進まなければ、全体最適の観点でデータは不完全なものになります。そこで、協力企業にも協力いただき、「KOM-MICS」を使い、コマツ部品の製造プロセスの見える化と改善を進めて行きました。
2019年にコマツの当時の会長から、「日本のものづくりを支えている中小企業にも「KOM-MICS」を使用してもらい、日本を元気にしていこう」という指示があり、一般販売が決まりました。社外にも開かれたオープンなプラットフォームにしていこうと、八子さんからコンサルティングを受けながら、どうやって市場に出せるかを検討し、サブスクリプション型販売モデルの導入など、価格面やマーケティング施策を立案して、2021年にクオリカから販売を開始したのです。
新入社員研修でタイムスタディ(どの工程のどの加工に何分間の時間がかかっているのかをストップウォッチで測る)が行われていたのですが、あるとき研修を終えた若手社員が、機械の中にパソコンが入っていますから、機械にいつ何が起こったのかを問い合わせればデータですべてを吸い上げられるのに、なんて無駄な作業をさせるんだ、と愕然としていました。それで2013年から開発が始まったのが「KOM-MICS」です。
コマツの部品の多くは社外の協力企業によるものですから、社外の工場も見える化が進まなければ、全体最適の観点でデータは不完全なものになります。そこで、協力企業にも協力いただき、「KOM-MICS」を使い、コマツ部品の製造プロセスの見える化と改善を進めて行きました。
2019年にコマツの当時の会長から、「日本のものづくりを支えている中小企業にも「KOM-MICS」を使用してもらい、日本を元気にしていこう」という指示があり、一般販売が決まりました。社外にも開かれたオープンなプラットフォームにしていこうと、八子さんからコンサルティングを受けながら、どうやって市場に出せるかを検討し、サブスクリプション型販売モデルの導入など、価格面やマーケティング施策を立案して、2021年にクオリカから販売を開始したのです。
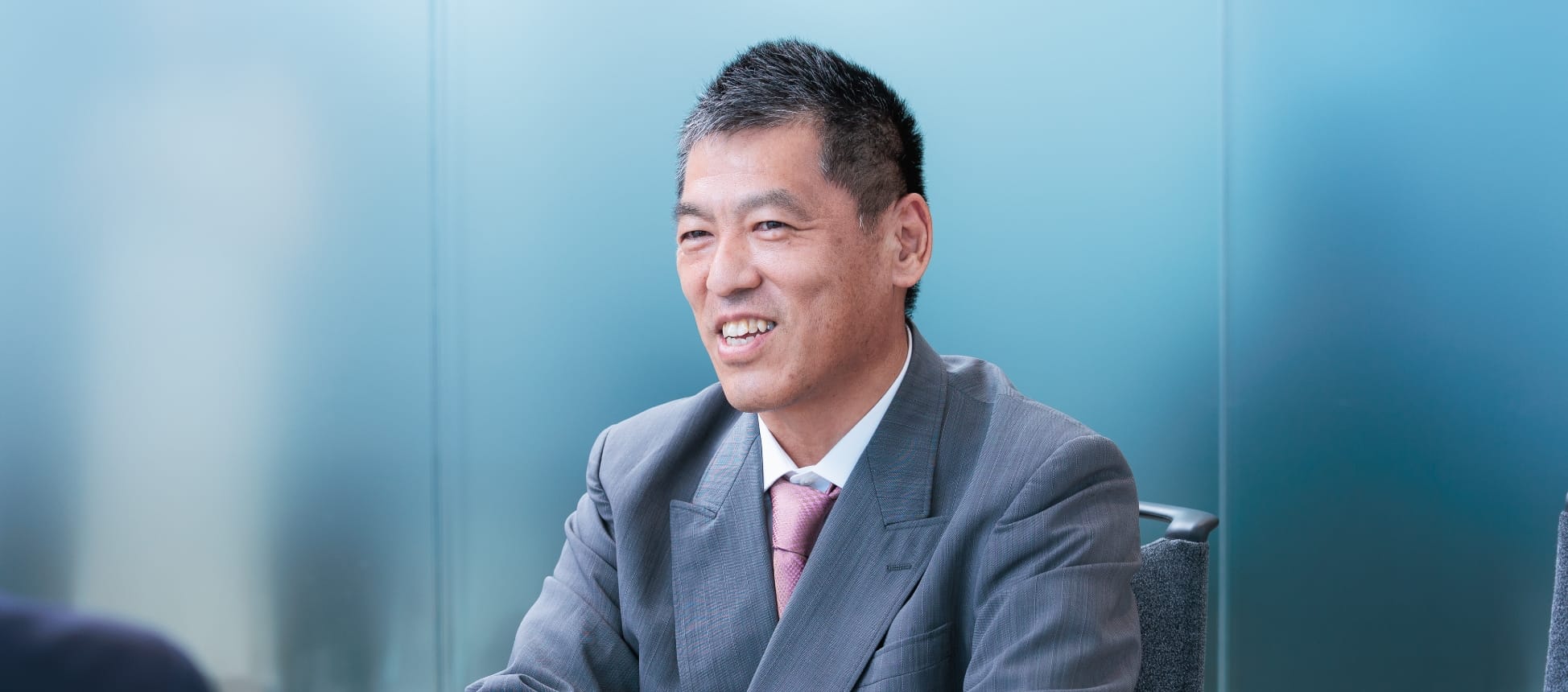
販売を開始してから何か気づいたことはありましたか?
名畑
一般販売が始まり、さまざまな企業の現場に足を運ばせていただくようになって気がついたのは、本当に現場には「データが無い」ということです。もともとデータをアウトプットできるように設計されたラインは問題ないのですが、通信機能はあるが単独で設置されてつながっていない機械、そもそも情報を吐き出してくれない機械など、情報を取り出す発想がない機械が多くありました。全体最適の観点でデータを分析するには、当然ながらすべての機械からデータを取得しなければ最適化できません。
そこで、標準の「KOM-MICS」でつながる機械だけでなく、情報量は少ないですが、バーコード、稼働を知らせる三色灯や電流計の外部センサーなどからも情報が取れるようにして、全体最適の施策を打つ素地を作っているところです。その結果、例えばこれまで班長しか知らなかった「昨日はどんな作業をしたのか」といった情報を誰もが見えるようになってきました。
そこで、標準の「KOM-MICS」でつながる機械だけでなく、情報量は少ないですが、バーコード、稼働を知らせる三色灯や電流計の外部センサーなどからも情報が取れるようにして、全体最適の施策を打つ素地を作っているところです。その結果、例えばこれまで班長しか知らなかった「昨日はどんな作業をしたのか」といった情報を誰もが見えるようになってきました。
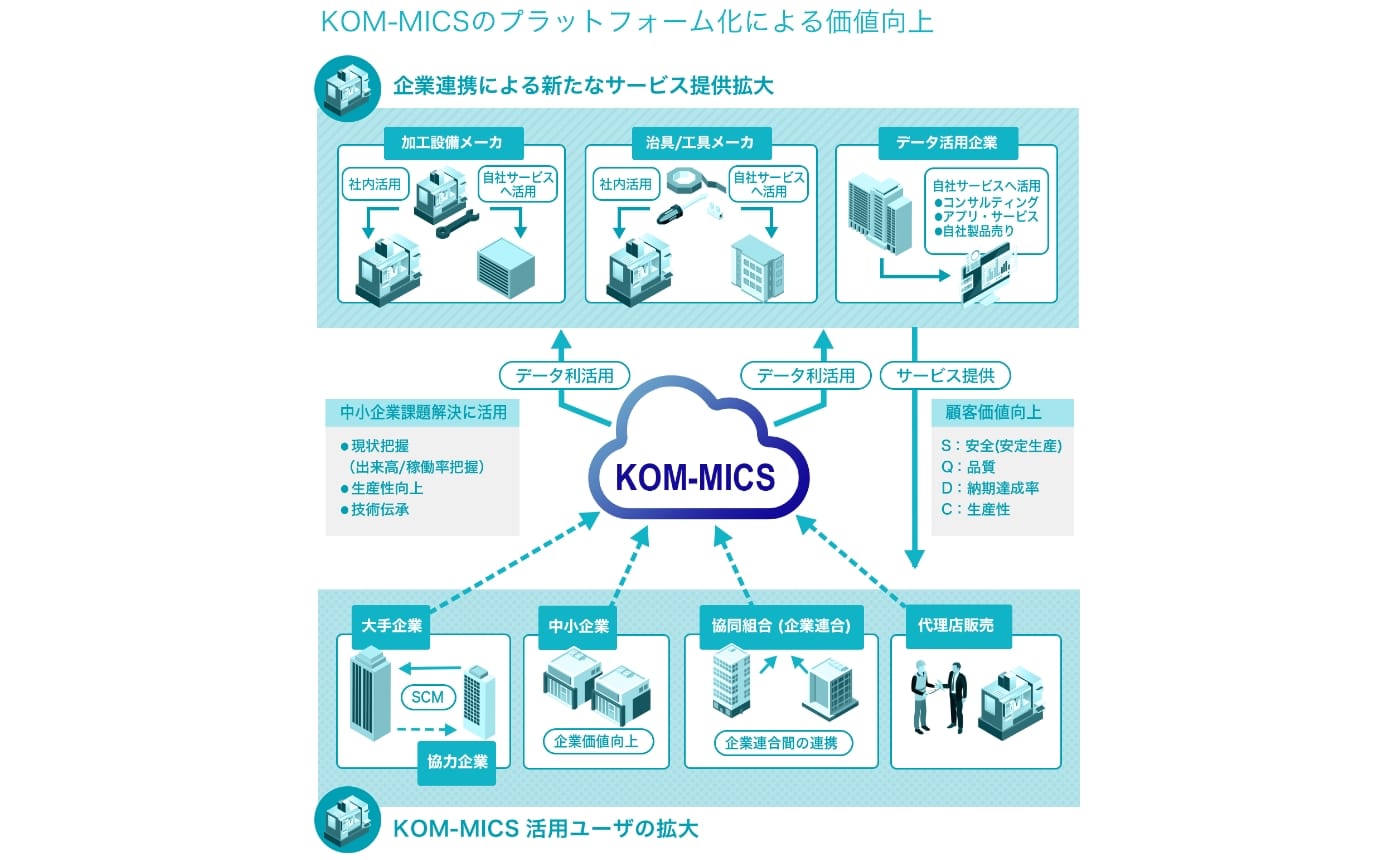
「効果やリターンを実感してようやく本格的にDXが進むようになる」
「KOM-MICS」を活用したDX支援は現在どこまで進んでいるのでしょうか。
名畑
現在「KOM-MICS」は、かなり古い機械にまで対応ができるようになりました。さらに検査データも含めて情報を取得することで、入口から出口まで、製造工程の全体が見える化できるように改良を重ねました。
DXを支援するにあたり、多くの中小企業には、儲かることがまず大事だと認識していただくことが重要です。全ての機械からデータを取得できるようにするために、いきなり数百万円もの金額を投資できる中小企業は多くありません。サブスクリプション型の販売プランを用意したのもそのためです。まずは1つの機械に導入してもらい、現場がラクになり、2時間の残業をせずとも済むようになる。その効果を体験していただいて初めて、全体最適の生産管理の計画を練るという、次のフェーズの重要性を理解していただけるようになるのです。
加えて、使用している電気の量からCO2(二酸化炭素)の排出量を算出できるため、環境問題に先進的なヨーロッパへも輸出ができるようになります。世界中から仕事が来れば、幸せな企業が増えていきます。「KOM-MICS」を導入すれば、マーケット拡大の恩恵を享受できることを実感していただきたいです。
DXを支援するにあたり、多くの中小企業には、儲かることがまず大事だと認識していただくことが重要です。全ての機械からデータを取得できるようにするために、いきなり数百万円もの金額を投資できる中小企業は多くありません。サブスクリプション型の販売プランを用意したのもそのためです。まずは1つの機械に導入してもらい、現場がラクになり、2時間の残業をせずとも済むようになる。その効果を体験していただいて初めて、全体最適の生産管理の計画を練るという、次のフェーズの重要性を理解していただけるようになるのです。
加えて、使用している電気の量からCO2(二酸化炭素)の排出量を算出できるため、環境問題に先進的なヨーロッパへも輸出ができるようになります。世界中から仕事が来れば、幸せな企業が増えていきます。「KOM-MICS」を導入すれば、マーケット拡大の恩恵を享受できることを実感していただきたいです。
八子さんは製造業のコンサルティングにおいて、どのような取り組みが多いのでしょうか。
八子
大きく2つのパターンに分かれています。1つは、すでにデータが取得済みで、見える化できているために、データを社外に販売できるような企業です。売上規模で言うと、年間数百億円以上の企業が、データ活用のフェーズに到達している印象です。
一方、それよりも規模の小さな企業では、紙の帳票や伝票を無くすためのペーパーレス化や、どの設備が稼働しているのか、在庫量や在庫のありか、といったデータの見える化のフェーズがまだまだ完了していない印象です。ここを乗り越えることが、DXフェーズへの移行の第一歩です。
データを見える化し、全体最適化すれば、少なくとも1〜2%は生産性が改善します。月商10億円の企業なら、数か月後には数千万円分リターンがあって残業代も減らせます。ですが、1千万円を超える投資にはなかなか腰が重くなってしまうものなんですね。
一方、それよりも規模の小さな企業では、紙の帳票や伝票を無くすためのペーパーレス化や、どの設備が稼働しているのか、在庫量や在庫のありか、といったデータの見える化のフェーズがまだまだ完了していない印象です。ここを乗り越えることが、DXフェーズへの移行の第一歩です。
データを見える化し、全体最適化すれば、少なくとも1〜2%は生産性が改善します。月商10億円の企業なら、数か月後には数千万円分リターンがあって残業代も減らせます。ですが、1千万円を超える投資にはなかなか腰が重くなってしまうものなんですね。
名畑
「KOM-MICS」も、導入していただくために工夫をしました。トライアル導入というサービスをご用意して、専用端末などハードの費用はいただかずに、ソフトウェアの契約も年契約でなく、単月でも可能にしたんです。すると、数万円の導入コストで運用できますから、3か月後には収支にプラスが出始めます。初めはできない理由をたくさん考えてしまうのですが、投資した金額以上に利益が出るとデジタル化への意欲が高まるのです。
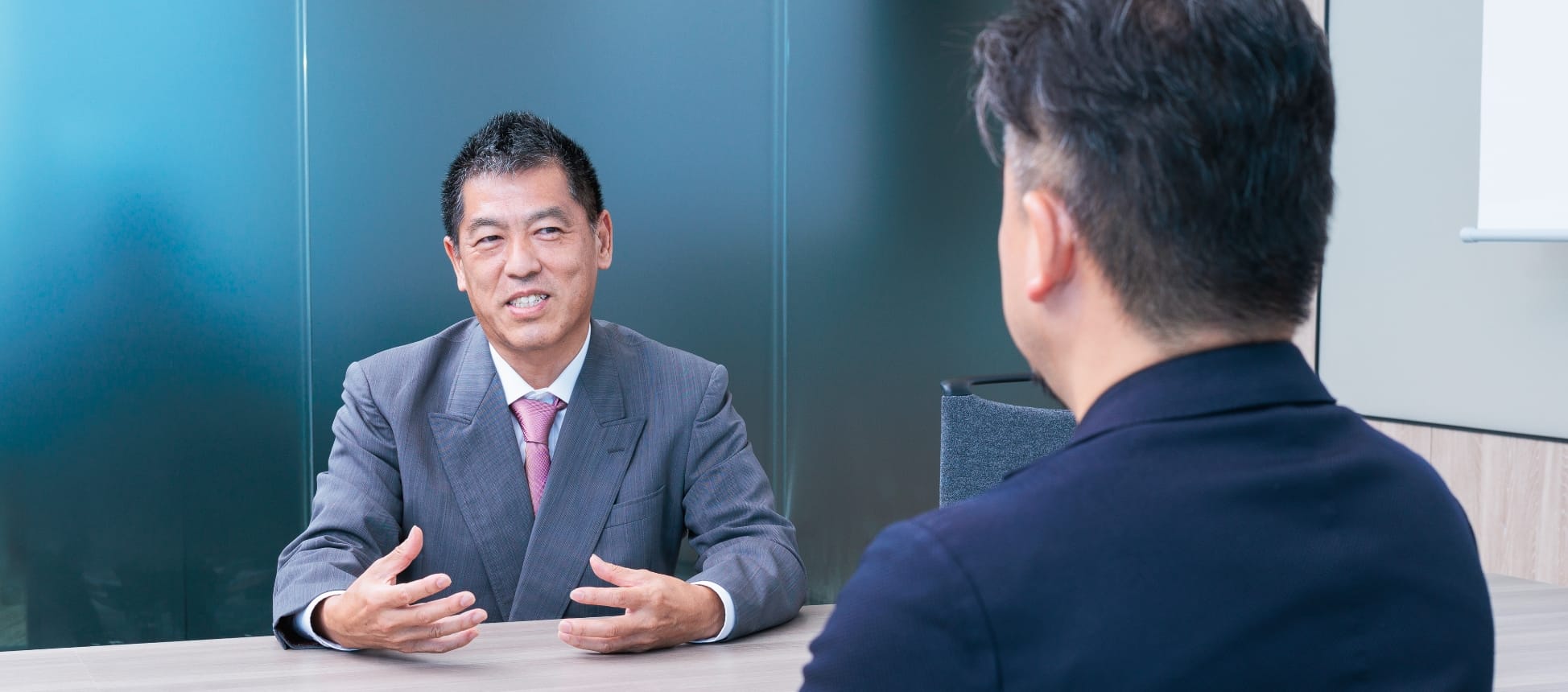
「生産性向上最大の課題は、人の労働力に頼っていること」
製造業のDXは今後、どのように発展していくと予想しますか?
名畑
DXとは変革を指すことは、冒頭に八子さんがおっしゃった通りです。ものづくりのしやすさや製造コストの低減などの効果が見えた次は、市場ニーズや商品力を見るフェーズへ。さらに、新しい価値を生み出すためにどのような商品を作れば良いのか、と階段を上るようにデジタル化からDXへとフェーズが移行していきます。
「KOM-MICS」を通じ、“生まれの品質”(保存された加工時の力や履歴データ、検査データから、個別の部品に紐付けされる品質)と、製品から入手できる使われ方情報、損傷情報を比較することで、部品の耐久性などの品質も見えるようになれば、改善が行われ、商品の価値が上がっていきます。さらに、納品までの物流上のリードタイムや、船積みされる現場の効率改善も必要であることが見えてきます。
しかし、物流も含めた大きなサプライチェーン全体を最適化させる改善活動は、「KOM-MICS」だけでは難しいです。他の物流プラットフォームと「KOM-MICS」を連携させることで、お客様から全体が見えるようになり、新しい価値を生み出す商品開発につなげられる、といったことが可能になる。例えば、より移送コストのかからないコンパクトな商品を、より短い期間で作れるようになるかもしれません。
「KOM-MICS」を通じ、“生まれの品質”(保存された加工時の力や履歴データ、検査データから、個別の部品に紐付けされる品質)と、製品から入手できる使われ方情報、損傷情報を比較することで、部品の耐久性などの品質も見えるようになれば、改善が行われ、商品の価値が上がっていきます。さらに、納品までの物流上のリードタイムや、船積みされる現場の効率改善も必要であることが見えてきます。
しかし、物流も含めた大きなサプライチェーン全体を最適化させる改善活動は、「KOM-MICS」だけでは難しいです。他の物流プラットフォームと「KOM-MICS」を連携させることで、お客様から全体が見えるようになり、新しい価値を生み出す商品開発につなげられる、といったことが可能になる。例えば、より移送コストのかからないコンパクトな商品を、より短い期間で作れるようになるかもしれません。
八子
私は物事の境界には必ず課題があると考えていますが、まさにその製造業と物流をつなぐ境界にも、課題は存在します。ほかにも、リソースの豊富な企業とそうでない企業、スピードの早い企業と遅い企業、などの境界がありますが、その境界をデジタルでつなぐと、やがてギャップが解消されてフラットになっていくはずです。
その際には、水が高いほうから低い方へ流れるようではなく、高い方向に逆流してフラットになるようにしなければいけません。そうしてパフォーマンスを高くするには、人間が感性で捉えている部分を数値で捉え、データで語れるようになることが重要だと考えています。
今後、生産人口が減っていく日本において、生産性を今よりも3倍は上げる必要があります。今はどこも人手不足の人材採用難で、商品に需要があっても増産ができない。生産性を向上させるしか道はなく、そのためにはデジタルを活用するしかありません。
デジタル活用をすれば、設備を必要に応じてオンデマンドで稼働させられるようになり、必要なときに必要なだけ人を連れてこられるようになります。すべてがオンデマンド型になり、欲しいときに欲しい分だけ活用できる。モノを作るときだけ工場を稼働できれば、温室効果ガスの排出だって抑えられるのです。
その際には、水が高いほうから低い方へ流れるようではなく、高い方向に逆流してフラットになるようにしなければいけません。そうしてパフォーマンスを高くするには、人間が感性で捉えている部分を数値で捉え、データで語れるようになることが重要だと考えています。
今後、生産人口が減っていく日本において、生産性を今よりも3倍は上げる必要があります。今はどこも人手不足の人材採用難で、商品に需要があっても増産ができない。生産性を向上させるしか道はなく、そのためにはデジタルを活用するしかありません。
デジタル活用をすれば、設備を必要に応じてオンデマンドで稼働させられるようになり、必要なときに必要なだけ人を連れてこられるようになります。すべてがオンデマンド型になり、欲しいときに欲しい分だけ活用できる。モノを作るときだけ工場を稼働できれば、温室効果ガスの排出だって抑えられるのです。
名畑
おっしゃるとおり、今の最大の課題は、人の労働力に頼っている部分です。24時間稼働している工場でも、「KOM-MICS」でデータを測ると、さほど稼働していない時間は少なからずあります。価値を生んでいる時間はせいぜい半分の12時間。あとは、待ち時間や移動時間など非効率に使われています。
人の労力をデジタルに置き換え、自動化し、人の判断が必要なときだけオンラインでタイムリーに判断ができれば、遠隔地からでも、複数のメンバーがデータと業務をシェアできるわけです。現場の生データを吸い上げて、その改善アプリとして「KOM-MICS」を活用していただく。そのパートナーをどんどん増やしていければと考えています。
人の労力をデジタルに置き換え、自動化し、人の判断が必要なときだけオンラインでタイムリーに判断ができれば、遠隔地からでも、複数のメンバーがデータと業務をシェアできるわけです。現場の生データを吸い上げて、その改善アプリとして「KOM-MICS」を活用していただく。そのパートナーをどんどん増やしていければと考えています。
※本記事の内容は、2023年8月21日時点のものです。
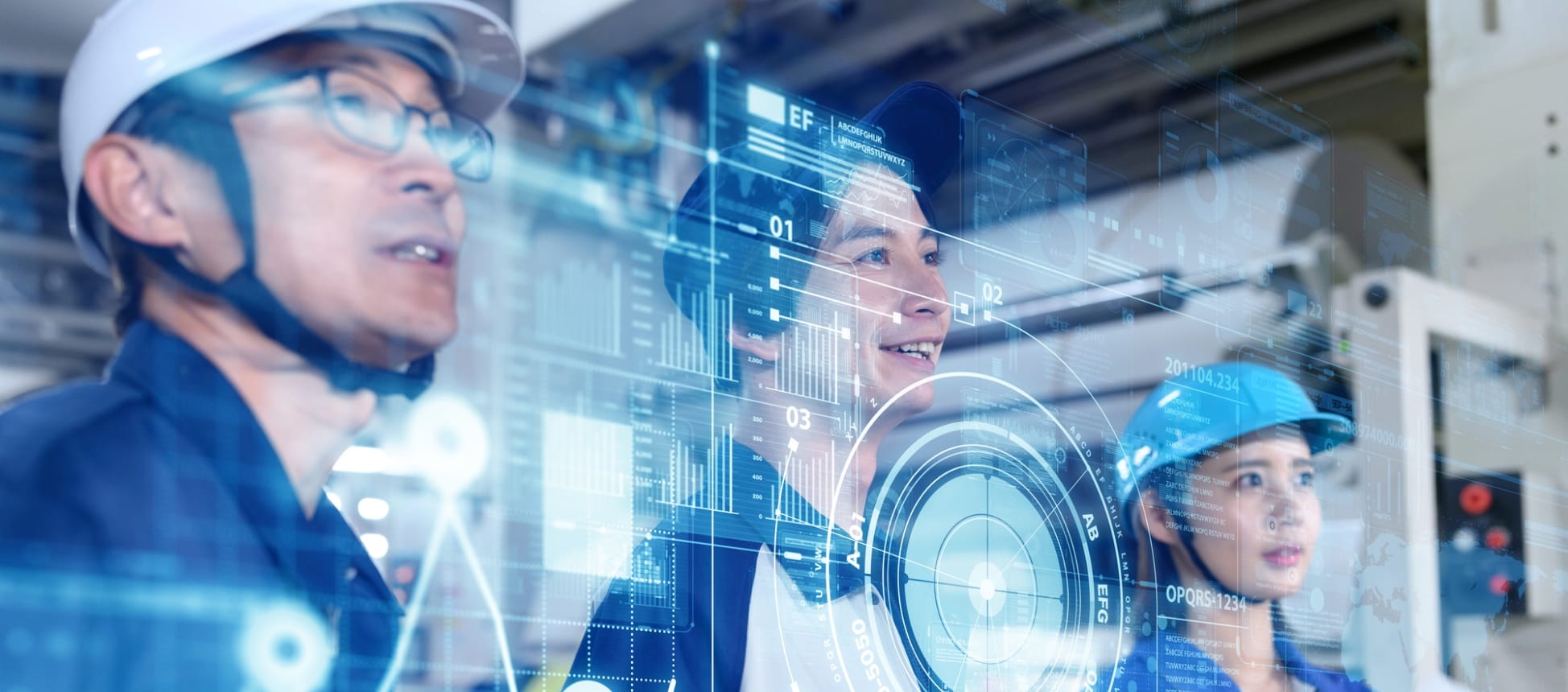
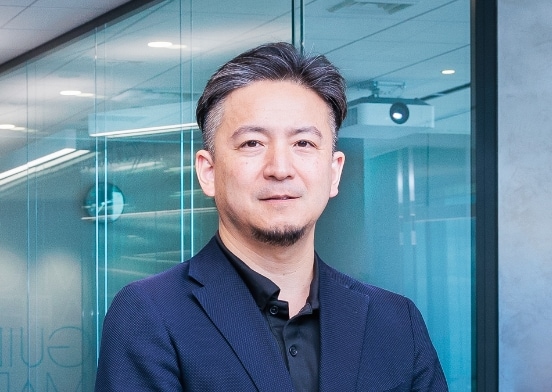
八子 知礼Tomonori Yako
株式会社INDUSTRIAL-X代表取締役CEO1997年松下電工(現パナソニック)入社、宅内組み込み型の情報配線機器の設計開発から製造移管および介護機器の商品企画開発に従事し、製造業の上流から下流までを一通り経験。その後、複数のコンサルティング企業に勤務した後、2016年4月より(株)ウフルに参画、様々なエコシステム形成に貢献。2019年4月に(株)INDUSTRIAL-Xを起業、代表取締役に就任(現職)。クラウドやIoT、DXコンサルタントとして多数の企業支援経験を有する。著書に「図解クラウド早わかり」「DX CX SX」など。
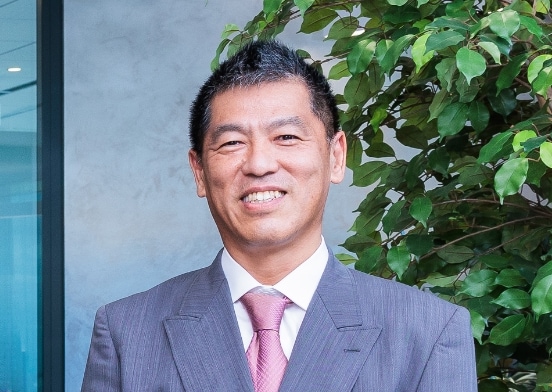
名畑 英二Eiji Nabata
クオリカ株式会社ビジネスイノベーション事業部
副事業部長1992年に株式会社小松製作所に入社。鋳造、熱処理、溶接の解析技術の研究開発を行った後、上流工程の建設機械の設計開発を経験する。2006年から機械加工プロセスの改善技術および加工装置の研究開発に携わり、2019年に「コマツのつながる工場システムKOM-MICS」で、ものづくり日本大賞の内閣総理大臣賞を受賞。2021年10月より、クオリカ株式会社にてKOM-MICS事業の立上げに従事。
副事業部長1992年に株式会社小松製作所に入社。鋳造、熱処理、溶接の解析技術の研究開発を行った後、上流工程の建設機械の設計開発を経験する。2006年から機械加工プロセスの改善技術および加工装置の研究開発に携わり、2019年に「コマツのつながる工場システムKOM-MICS」で、ものづくり日本大賞の内閣総理大臣賞を受賞。2021年10月より、クオリカ株式会社にてKOM-MICS事業の立上げに従事。
TISインテックグループ社員と
外部有識者の方が対談を行うコーナーです。
社会課題の解決のために
叶えたい願いと想いを語るコーナーです。
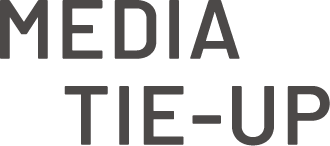
タイアップ記事をご紹介します。
TISインテックグループの
取り組みについて発信するWEBマガジン
(以下、敬称略)
IT化・デジタル化とは、例えばCDだったものを音楽配信にしたり、紙でのFAX送信をメールに置き換えたりと、物理的な手段をデジタルに代替することです。
一方のDXは、すでにデジタル化がなされている前提の上で、業務全体や組織、商材、ビジネスモデルを変革していくことを指します。デジタルを活用してあなたの企業はどうなりたいですか、と問われているのがDXです。